The pandemic ushered in a rapid acceleration of digital transformation initiatives in the industrial sector, and automation is one of them.
Important data published by Fortune Business Insight, indicates that the global industrial automation market reached $168.81 billion in 2019 and is expected to reach $326.14 billion by 2027.
The interest of organizations in automations is due to the many benefits they bring them, advantages in many aspects, but especially in terms of savings in time, errors and costs, as well as multiple benefits.
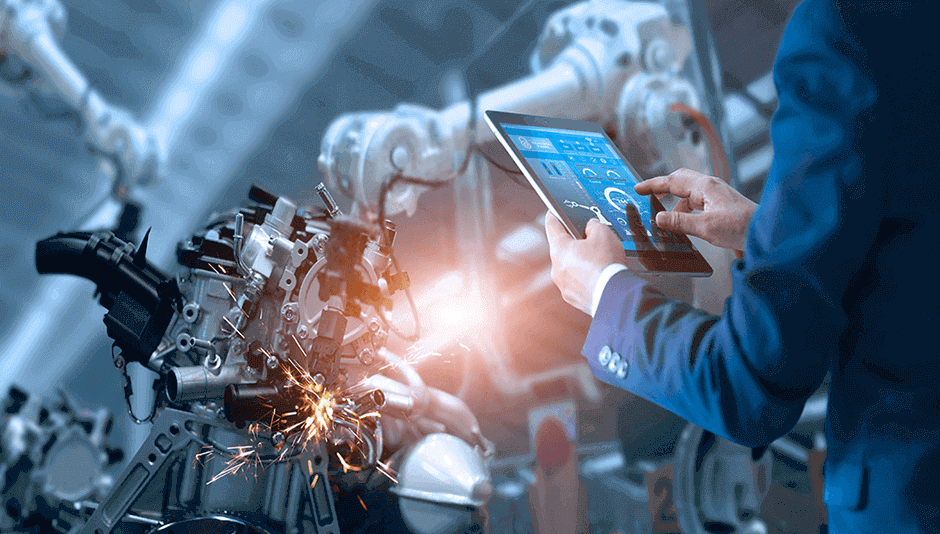
What is automation?
Before going into detail, it is important to understand what industrial automation is, which is defined as the use of technologies for the control and monitoring of processes, replacing manual tasks, generally repetitive functions, with automated functions in which human intervention is scarce, and in some cases null.
There are two environments in which industrial automation could be applied: OT environments, or operating environments, in which traditional manufacturing tasks are performed; and IT environments, or information environments, focused on computers and their software.
One of the main objectives involves improving working times, productivity, process quality and the company’s competitiveness. This last point is of great relevance, since globalization has favored imports and exports of products, making the automation process a key element to remain competitive and efficient with respect to competitors.
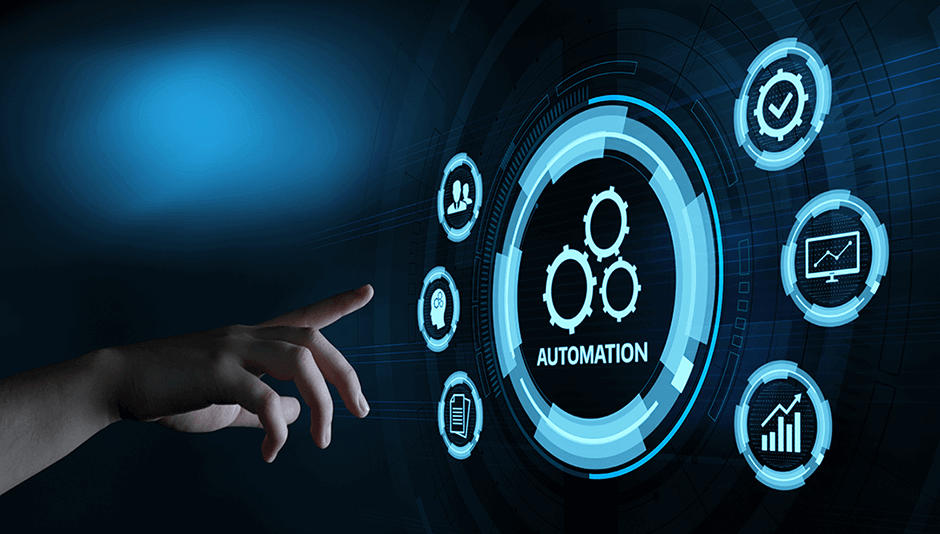
Types of industrial automation
Now that we have talked a little about the definition of an industrial automation system, we should highlight the 4 types most commonly used today by companies in their processes:
- Fixed automation system: based on special equipment that is used to streamline specific processes. Industries that have to produce stable and sustainable product designs over a long period of time opt for fixed automated systems.
- Programmable automation system: this type of technology is used to manufacture products in batches, it is designed to facilitate product changeover, however, the reprogramming process is time-consuming.
- Flexible automation system: this is a more sophisticated and refined form of programmable automation, its difference lies in the fact that it allows the equipment to be changed automatically and quickly. A product mix can be produced consistently without wasting time.
- Integrated automation system: a set of independent machines, processes and data, working synchronously under the control of a single control system. Computer-controlled tools and machines, robots, cranes and conveyor belts can be integrated with each other using programming and production control.
9 benefits of automation
The reason why organizations implement different industrial automation systems. Due to the wide variety of benefits it brings, let’s know some of them:
- Productivity: improves productivity, reduces assembly times, enabling continuous mass production 24/7
- Quality: eliminates human error. Improving the quality and homogeneity of the products, without affecting the yield after several hours of work
- Greater consistency: it has greater durability, stability and solidity, working at a constant and continuous rate
- Flexibility: reprogramming a robot or a machine is a simple and fast process, providing greater flexibility in the production process
- More accurate information: automation of data collection improves accuracy, enabling business decision makers to make better decisions
- Safety: it is safer to use robots in production lines with hazardous working conditions for humans
- Reduce costs: although the initial investment of the systems is high. Thanks to this technology it is possible to reduce data analysis costs, reducing machine failures and service interruptions
- Better working conditions: workers dedicate their time to performing tasks with high added value.
- Enhances human capability: systems not only perform tasks that a human being would do. But also functions that exceed a person’s capabilities.
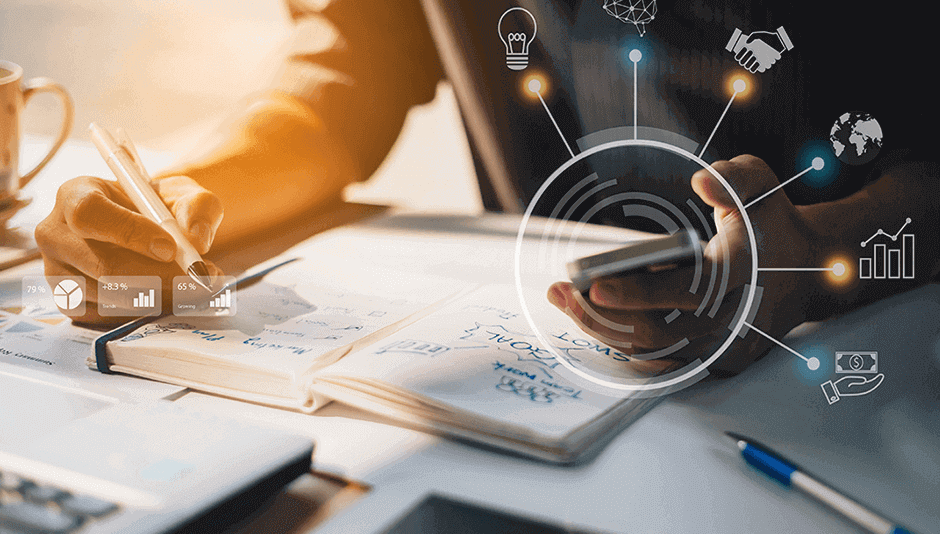
Examples of industrial automation most commonly used today
- Assembly lines: with machinery that deals with the continuous assembly of parts and their fastening, screwing, welding, etc. As in the automotive industry
- Addition of components: with systems that create chemical or food preparations. Through the progressive incorporation of different ingredients in the assigned proportions. As in the cosmetics industry
- Packaging: with technology that is capable of handling different types of packaging materials. Even the most fragile (e.g. glass), to configure a perfect packaging, including labeling. Like the food industry
As we have seen, industrial automation systems bring different benefits to organizations.Their future seems to be very promising.
Industrial robots of the future will be multifunctional so that the same machine can be used for different purposes. They will have many associated capabilities, such as decision making, self-diagnostics and predictive maintenance.
Thanks to industrial automation, factories future will be more efficient in the use of energy, raw materials and human resources. Experience so far has shown that automation will not generate mass unemployment. On the contrary, the use of robots will create more jobs. In which working together will be more efficient and productive.
Do you want to apply an automation process to your company but don’t know where to start? At Interfaz we are here to help you.
Resources: Automation Industrial Tendencies 2020 | Fortune Business Insights | Benefits of having an Industrial Automation System